ENVIRONMENT
Environmentally-Friendly manufacturing process
Since we consume electricity mainly in our manufacturing processes, we promote activities focusing on utilizing natural energy-derived electricity and improving the efficiency of its use.
Here are some of our initiatives toward environmentally friendly manufacturing process.
Environmentally-Friendly facilities
Introduced LED lighting at our main plant
Since the installation of LED lighting in the new main factory constructed in April 2017, our old factory and head office have also completed the conversion to LED lighting.
We will continuously make efforts to improve the energy efficiency of our entire plant, including the introduction of energy-efficient equipment.
Efficient use of natural energy
Since the installation of solar panels on the building roofs at our new main factory constructed in April 2017, we have also installed solar panels on our Research & Development Center and service factory building located at our main plant, with a total of 871 kW of solar panels in operation. In addition, our subsidiary, Dalian Teikoku Canned Motor Pump Co., Ltd., has installed a total of 1,421 kW of solar panels on both its new and existing factories in line with the construction of the new factory. Through this initiative, we strive to make efficient use of natural energy and reduce our environmental impact.
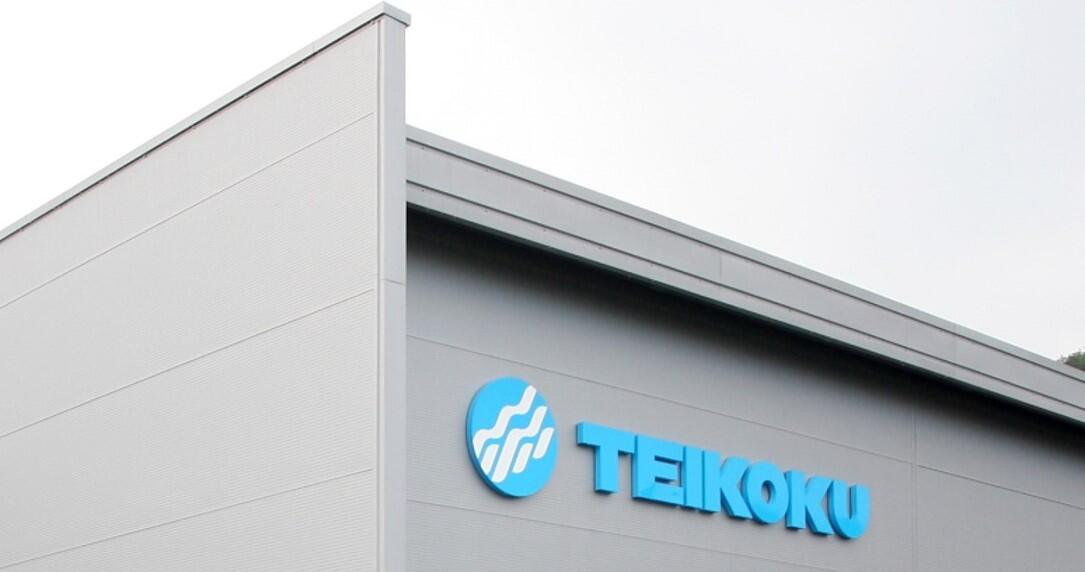
Improved efficiency of air conditioning and energy
For constructing the exterior walls of our new main factory, we have used building materials with high thermal insulating properties. In addition, we use air-conveying fans to improve air conditioning efficiency and reduce energy consumption to cut down CO2 emissions.
We also work to improve the energy efficiency of our factories by introducing ultra-high efficiency transformers.
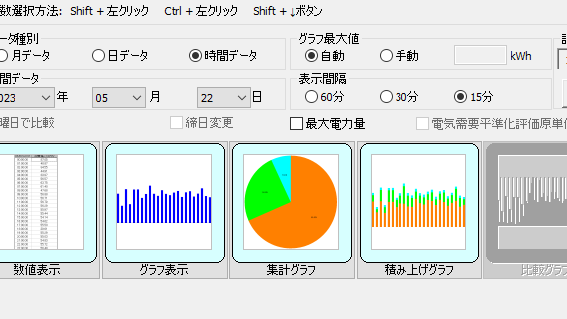
Introduction of a plant-wide energy management system
We can manage overall energy usage and implement effective power-saving measures by installing energy demand monitors that visualize energy usage in each area in our main plant.
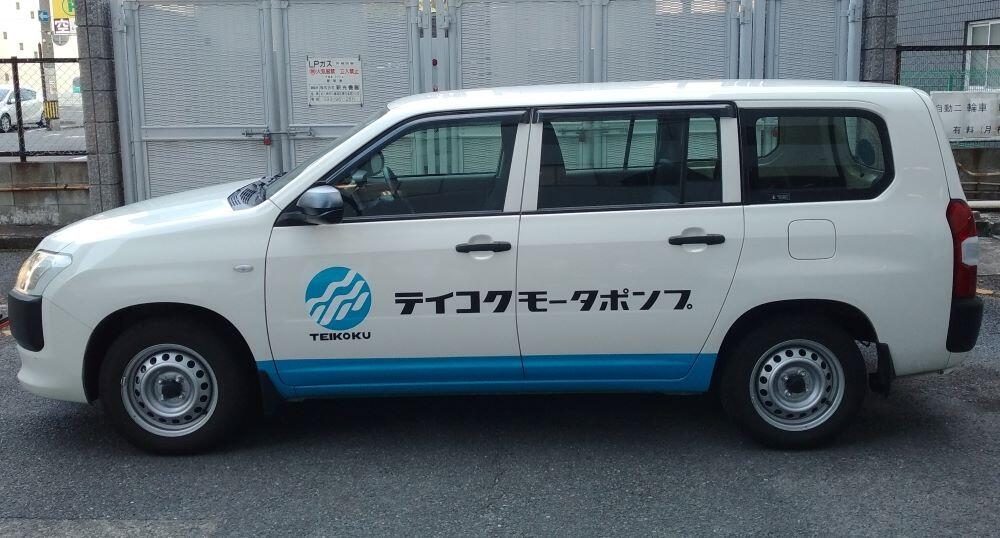
Introduction of hybrid vehicles in company fleet
We started converting company vehicles to hybrid since FY2021.
Of our 34 company vehicles, we have gradually been switching them to hybrid vehicles from those scheduled for renewal. As of March 31, 2025, approximately 40% of our company vehicles had been converted to hybrid vehicles.
Introduction of CO2-free electricity
Our Tokyo Sales Office switched its electricity menu and introduced CO2-free electricity in July 2024. As a result, CO2 emissions from electricity consumption at the Tokyo Sales Office have been reduced by approximately 8.0 t compared to the previous fiscal year.
Noise reduction measures for surrounding area
To minimize the noise impact on areas surrounding our main plant, we have installed noise-prone equipment such as generators and compressors in soundproof buildings.
Water saving measures
We have implemented a water recovery and circulation system for our pump performance testing facilities to reduce tap water usage and minimize wastewater generation.
Water Usage (domestic manufacturing and service sites)
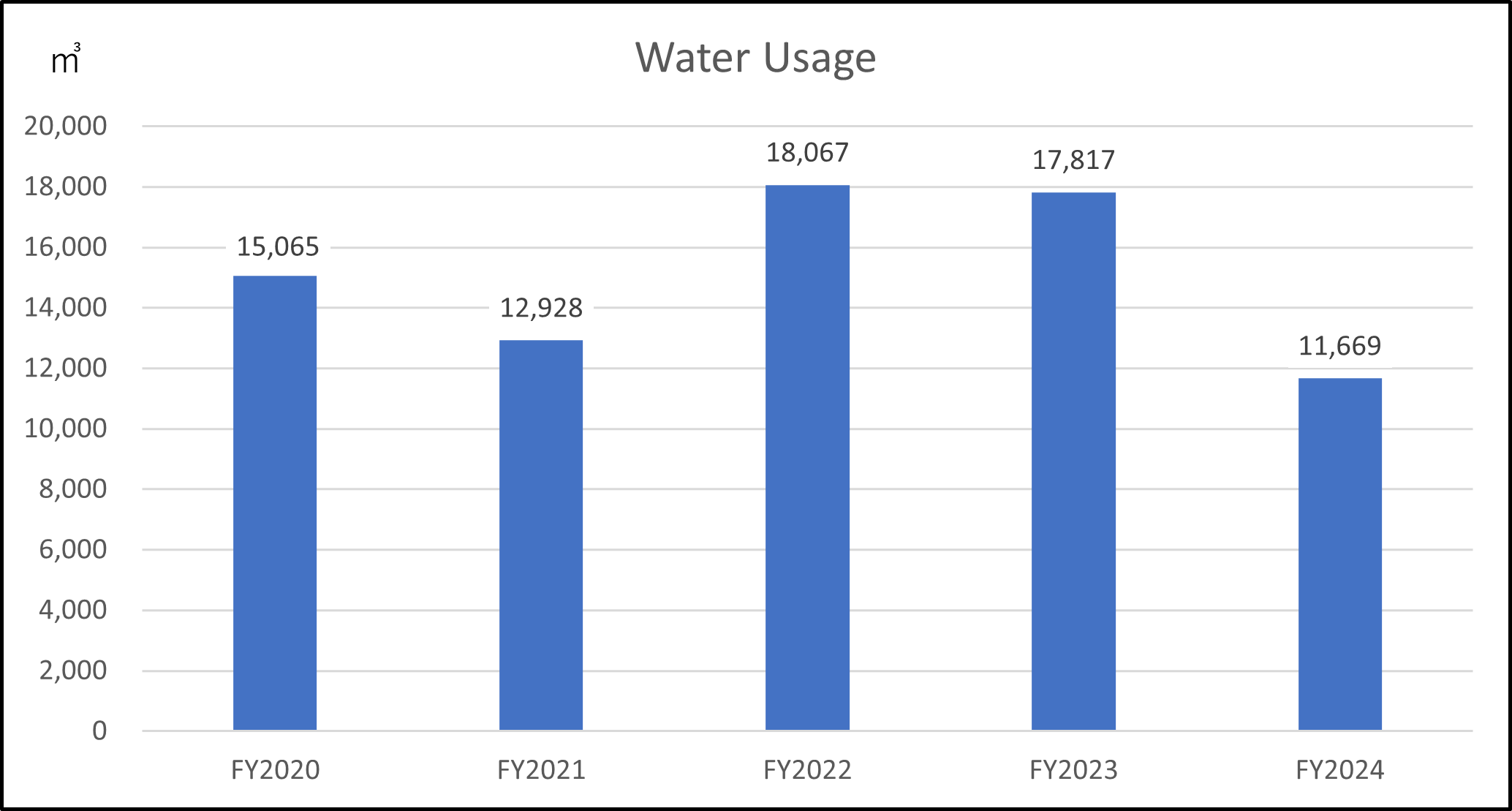